
Lean transformation and digitalization go hand in hand. In the podcast, Tobias Kehrer and Falk Hieber explain how Carl Stahl GmbH benefited during the pandemic.
Lean Transformation: The roots go deep
Carl Stahl took its first steps in the area of lean back in 2007. “At that time, after strong growth and corresponding diversification, we found that our organization was reaching its limits,” recalls Managing Director Tobias Kehrer.
A highly branched organizational chart, wide management scope, long lead times and many interfaces led to the decision to change something. Leadership decided to start by transforming one product area using Lean Management principles: “After we reduced inventory as a first step, liquidity and lead times improved in that area.”


After initial success with lean, the road got rockier
The company wanted to extend this success to all departments – and had to recognize that the transformation was not successful without outside help. “The road became rockier, but our path up to now has been filled with detours,” says Managing Director Kehrer, describing the course so far, which Staufen AG has been supporting for several years.
Now Carl Stahl is a BestPractice Partner of Staufen. Although the Lean Transformation is not yet complete, Tobias Kehrer is convinced that the company is on the right track: “We have now really reached the point where we can talk about Lean Transformation, have a roadmap and have achieved interim success.”
Lean und digital belong together
The two managers consider the interaction of lean and digital in the company a success. Because Carl Stahl recognized early on that digital ideas could support the principles and methods of Lean Management.
“We all sit at our computers every day; we use video calls. We do many things digitally. And when you’re dealing with lean processes, you can’t avoid dealing with digital topics,” says Tobias Kehrer.
I’ve never understood the competing view of lean and digital.
Tobias Kehrer, Managing Director, Carl Stahl GmbH
Shop Floor Management for more transparency
This has an impact on collaboration and the culture of the company. Today, employees give positive feedback when asked about issues such as transparency and communication within the company. Employee involvement in solving problems is on the rise. “We conclude that Shop Floor Management as a structured management tool has made a significant contribution to this,” says OD Manager Hieber.
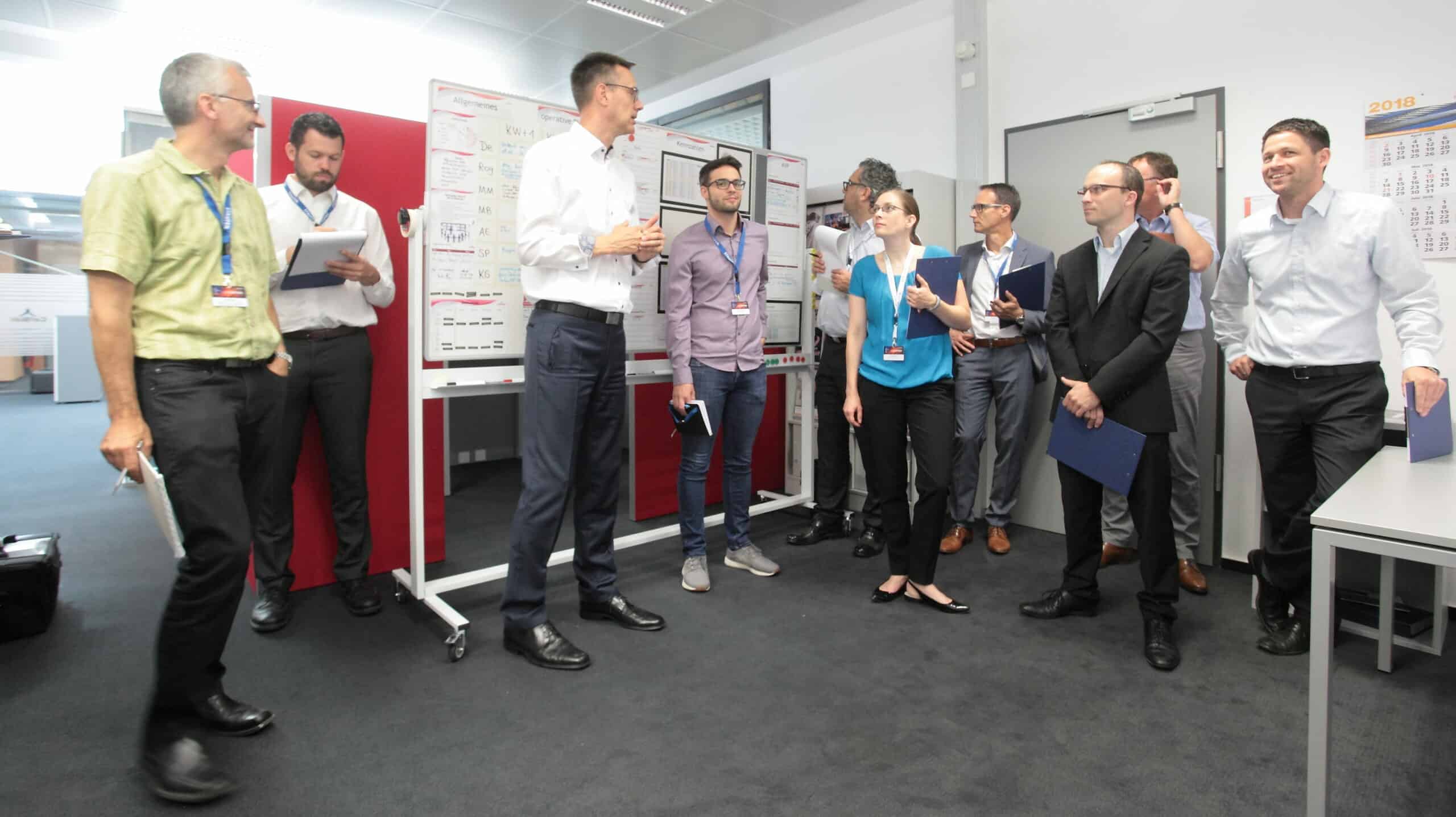
Navigating the pandemic with digital processes
Right at the beginning of the pandemic, the well-functioning interplay between lean and digital came to the rescue. From the beginning of the first lockdown, all employees who were not employed in production were able to work from home. In teams, they worked independently during this phase using virtual boards to maintain the workflow.
Contact among managers was maintained in daily virtual jour fixes. “As a result, we were also able to make decisions very quickly, enabling us to react to situations very quickly,” Tobias Kehrer recalls. Being digitally prepared, Lean Management and the resulting clear communication structure allowed management to take handle topics from the start. “And that certainly led to the fact that we also had slumps in terms of incoming orders and sales, but overall we came through this period very well economically.”
Guest
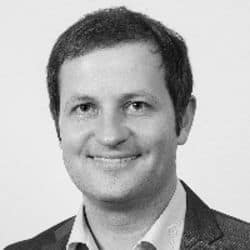
Tobias Kehrer
Managing Director
Carl Stahl GmbH
Moderation

Janice Köser
Academy Manager
Staufen AG
Guest

Falk Hieber
Head of Organizational Development
Carl Stahl GmbH
Seminar:
Lean Transformation and Digitalization hand in hand
In this seminar, we will answer why lean management is more relevant today than ever before and how you can use the advantages of digitalization for yourself. Learn how CARL STAHL has turned some of the biggest challenges on the lean journey into success factors. Stringent orientation on customer value, cross-functional lean management and above all: keep at it, come what may! The lean journey never ends, instead we open new chapters for you.

Best Practice Live
Exclusively for you, we are opening the gates to excellent businesses – our BestPractice partners. Benefit from case studies of successful businesses.
Read more
Digitalization & Industry 4.0
Intelligent Industry 4.0 production processes can be applied to accomplish a variety of objectives. These include achieving greater productivity and efficiency, fulfilling consumer specifications faster and more expediently, and developing brand-new industrial products and business models. Small and mid-sized companies often have a particular need for this kind of consulting and guidance.
Read more
Customer orientation despite strategy development and process optimization
“The customer is the main focus” and “the customer is king.” This is the motto of many companies. But in reality it is often a challenge to focus on the customer while also implementing sophisticated strategy development and process optimization. How do you manage to standardize your processes internally and at the same time remain capable of responding to customer needs in a flexible manner? Tobias Kehrer, Managing Director of Carl Stahl Süd GmbH, focuses on this question on a daily basis. He is responsible for ten sales and service locations in the rope, lifting and safety technology sector in Southern Germany. In order to cope with the lean transformation, he initiated the “ProcessEvolution” program at Carl Stahl. His advice on how to manage this balancing act between strategy development and process optimization is based on his experience in industry, but it can also be easily transferred to service companies.
Read more