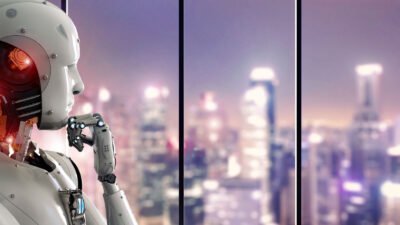
Large, orange and sitting behind a protective barrier – Germans’ idea of robots in the realm of work has not changed for years. Because of this, 71 percent of employees still see robots’ field of application, especially in industry, is for dangerous or physically demanding work. However, only 41 percent could imagine robots as service providers or service personnel, while only 14 percent could see them being used in nursing care applications. These are the results of a representative survey of more than 1,000 employees in Germany conducted by business consultancy Staufen.
“Our study shows that the overwhelming majority of employees – from all industries – still views robots as updated cargo cranes or fearless laser welders,” says Dr. Jochen Schlick, Senior Partner at Staufen Digital Neonex. “Cooperative applications and flexible tasks such as in indirect areas, the service or health care sectors, however, continue to be completely underestimated or are entirely unknown.”
The rather simple idea of a “stupid robot” is likely to be a key reason that only a third of employees fear being trumped in the future in terms of precision and accuracy by a robot; this opinion is even only held by a quarter of employees in industry. “The fact that about half of employees see their own position as threatened by robots makes it clear how quickly ignorance becomes insecurity – even among well-trained specialists and academics,” says Senior Partner Schlick.
At the same time, Germany’s employees are open to the potential benefits of having a high-tech colleague. Almost three-quarters would like to have robots to alert them of their mistakes. Also, the majority of respondents appreciate the predictability and consistently high quality of robotic work. “As with digitization, executives are also in demand here,” says Industry 4.0 expert Schlick. “They must guide their employees into the new world of work, reduce fears and prejudices, and work with them to develop concrete application examples for using robots.”
Support for education and training could come from the private sector this year. For example, both e-commerce company Amazon and robot manufacturer Boston Dynamics plan to launch their first robots for household use on the market. In addition, it could help to make robots more human-like: According to a study by business consultancy Staufen together with Staufen Digital Neonex GmbH, half of employees want robots to have a face, arms and legs.
Save the date: NEXCON on February 28, 2019
NEXCON is an international, fully virtual congress on smart manufacturing. As part of the 15-hour live event, leading experts from well-known companies and institutions (including BASF, Daimler, Schaeffler Group and Fraunhofer IPA) will speak on current trends, developments and experiences in the fields of digital transformation, data analytics as well as augmented and virtual reality in an industrial field of application. In addition, established companies and innovative newcomers will be presenting themselves in the digital exhibition hall. The focus of NEXCON 2.0 is also on the combination of the German initiative “Industry 4.0” and the Chinese initiative “Made in China 2025.” Additional information on participants, exhibitors and partners can be found at:
More Information: STAUFEN.AG Kathrin Negele Blumenstr. 5 |
STAUFEN.DIGITAL NEONEX GmbH Maya Worm Königstr. 2
|
Press: Thöring & Stuhr – Partnerschaft für Kommunikationsberatung Arne Stuhr Mittelweg 142 |
About Staufen Digital Neonex GmbH – www.staufen-neonex.de
Staufen Digital Neonex GmbH is a subsidiary of Staufen AG and provides consulting services to medium-sized producers as they undergo digital transformation. In addition to pragmatic digital strategies for small and medium-sized enterprises, topics relating to smart factory, data science and digitization of product ranges and business models are also part of the program. Those involved can count on Staufen Digital Neonex as a steadfast partner. Uncertainty and any mistrust are reduced through customized qualification programs. Even when it comes to smart factories, one thing holds true for Staufen: People make the difference.
About Staufen AG – www.staufen.ag
Inside every company there is an even better one. With this conviction, Staufen AG has been advising and qualifying companies and employees for more than 20 years. Markets are on the move – the competitive pressure is enormous. Staufen helps to quickly bring about the right changes, increase productivity, improve quality and increase innovative strength. With the appropriate strategies and methods, the international lean management consultancy ensures rapid and measurable success. In order to leverage the potential available in every company, Staufen consultants establish a lively and sustainable culture of change together with executives and employees. Staufen subsidiary Staufen Digital Neonex supports medium-sized industrial companies on their path to digital transformation. The Academy of Staufen AG also offers certified, practice-oriented training courses. Of the 13 international locations, more than 260 employees serve customers all over the world. In 2018, Staufen AG was recognized by “brand eins Wissen” as “Best Consultants” for the fifth year in a row. According to the renowned industry study “Hidden Champions 2018,” the consulting firm is Germany’s best lean management consultancy and was honored several times with the “Best of Consulting” award by the “Wirtschaftswoche” journal.