
Virtual BestPractice Tour
True to the motto “Travel educates!”, Staufen AG regularly takes entrepreneurs, executives and technical experts on a “lean expedition” as part of its BestPractice Tours. Successful owners and experienced managers, together with Staufen consultants, provide a glimpse behind the factory gates of excellent companies and serve as tour guides, answering questions such as: What does the introduction of Lean Management mean for a company? How can lean projects be optimally planned and implemented? Which key figures can be improved permanently through Lean Management?
The itinerary of the latest – in this case virtual – BestPractice tour included Rittal (Shanghai site, China), MTU Aero Engines (Munich site, Germany), Endress+Hauser (Pessano site, Italy) and TK Elevator (Guaíba, site, Brazil). Markus Franz, Senior Partner and Supervisory Board Member of Staufen AG, acted as moderator throughout the day, linking companies and various transformation stories which all had different focuses, but each led to the same conclusion: Inside every company there is an even better one!
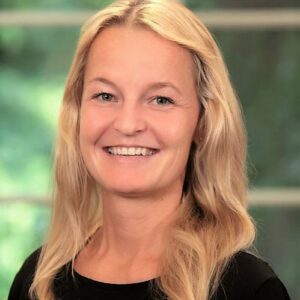

Michael Galler
Vice President Operations
Rittal Electro-Mechanical Technology (Shanghai) Co., Ltd

Michael Galler
Vice President OperationsRittal Electro-Mechanical Technology (Shanghai) Co., Ltd Read more
Station 1
Rittal on a “never-ending journey”
In Shanghai, Rittal GmbH, the largest company in the German Friedhelm Loh Group, provides the solutions of the future with a smart system architecture comprised of individual modules (enclosure, power distribution, climate control, IT infrastructure and software & service). With the goal of increasing productivity and surpassing in-house KPI benchmarks, the company set a lean course with Staufen Project Manager Jacee Cai. The corporate culture played a key role in this.
Michael Galler, Vice President Operations at Rittal China, sees successful lean implementation not as a self-contained process, but as a “never-ending journey” in which process excellence and leadership excellence are continually challenged and improved. Companies must be prepared to constantly question their culture, organization and structure: “Those who do not adapt will suffer the same fate as the dinosaurs. The key figures prove how successful Rittal has been in implementing Shop Floor Management and the underlying Lean Transformation. There are 13 KPI target marks, of which the Chinese subsidiary achieved significant improvements in twelve cases and at least slight improvements in one case.
Station 2
MTU Aero Engines soaring to new heights
Speed is in MTU Aero Engines’ corporate DNA. And as part of the Lean Transformation, internal communications are also at top speed. With support from Staufen AG, the company has introduced a Shop Floor Management system. The new exchange strengthens on-site problem solving, reduces subsequent schedule changes and increases transparency in production. As a result, the company can now act much faster. Because SFM was developed in close cooperation with the workforce, multipliers from within the company can carry the project further.
For the people responsible for lean at MTU, Michael Zaun (Head of Production Turbine Blades and Structural Components) and Matthias Plank (Team Leader Manufacturing Engineering), the shift towards lean has also proved its worth in the course of digitalization and during the Corona crisis. As part of the transformation process, it became apparent that processes needed to be adapted and simplified for the transition to the digital world. This paid off, he said, especially during the pandemic, because the organization was agile and adaptable to meet new demands.
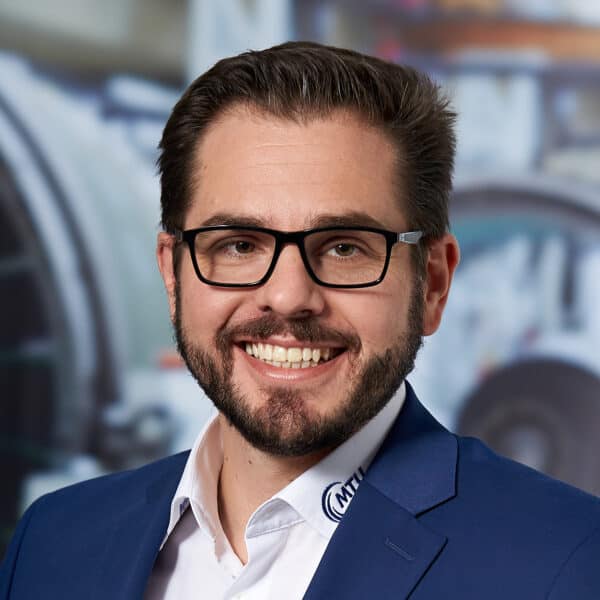
Michael Zaun
Head of Production Turbine Blades and Structural Components
MTU Aero Engines AG
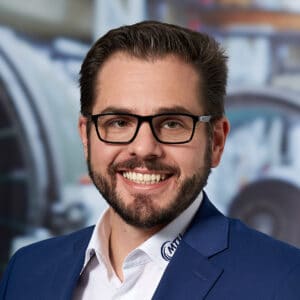
Michael Zaun
Head of Production Turbine Blades and Structural ComponentsMTU Aero Engines AG Read more

Gianfranco Migliarotti
CFO and HR Director
Endress+Hauser Sicestherm S.r.l.

Station 3
Endress+Hauser on the path to a new corporate culture
With a lot of enthusiasm and passion, Gianfranco Migliarotti in Pessano con Bornago is responsible for the SFM lean leadership transformation of Endress+Hauser.As CFO and HR Director, he knows the opportunities and challenges of the Italian division of the Swiss supplier of equipment for process engineering. Together with Giancarlo Oriani, General Manager of Staufen Italia, the production processes were converted to one-piece flow. Gianfranco Migliarotti saw a central challenge for this in the control system: “We implemented a new concept of a mini-factory and adapted the processes for agile teams.”
Behind the process adaptation is a change in corporate culture, which was given top priority as part of the SFM introduction: “We pay attention to values. But it is more important to move from values to culture. Managers in particular are called upon to set a good example and exemplify the new world of values. So actively listening, asking questions, answering questions, and acting as a facilitator, not a supervisor.” Introduction of the new Shop Floor Management was completed in just nine months. The transformation journey as a whole, however, Migliarotti said, is a lengthy one. For the Endress+Hauser manager, it is like having a newborn baby: “We have to feed our baby first, then it learns to walk, and we focus on good parenting. This is a very long process, and we are always straightforward and careful to convey values. That’s the most important part.”
Station 4
TK Elevator on track
Since 2014, TK Elevator’s Business Unit in Latin America promoted changes in the management of Manufacturing, aiming to improve the productivity of the elevator factory, located in Guaíba, Rio Grande do Sul. With the help of Dario Spinola, Managing Director of Staufen Táktica in Brazil, a Shop Floor Management roadmap was created, and the entire operation was made lean. Comparing the Brazilian elevator factory between 2014 and 2022, the Industrial Engineering Manager, Marco Felipe Assumpção, draws a clear conclusion: structure and order have become as visible as the new orientation of the employees.
Today, production is of the highest standard, from a state-of-the-art electrical manufacturing pavilion and clearly structured production. For example, the KPIs for operational excellence increased from 33.5 points in 2014/15 to 75 points today. The goal of improving production in Brazil has already been achieved, as stated by Marcelo Nery, Manufacturing President TK Elevator of the Business Unit Latin America: “Seven years ago, production and delivery were our priorities. However, I pay special attention to safety. We have made enormous progress and if we can guarantee safe production with no accidents, other advantages will certainly arise”.

Marcelo Nery
President MFG
Thyssenkrupp Elevadores

Conclusion
The four practical examples show that successful transformation is only possible through a holistic approach in which structures, processes and cultural aspects are jointly addressed. What is the best way to do this? Staufen Consultant Markus Franz has identified four core competencies for this: curiosity, skepticism, courage and humor. After all, the transformation must not only be successful, it should also bring joy.
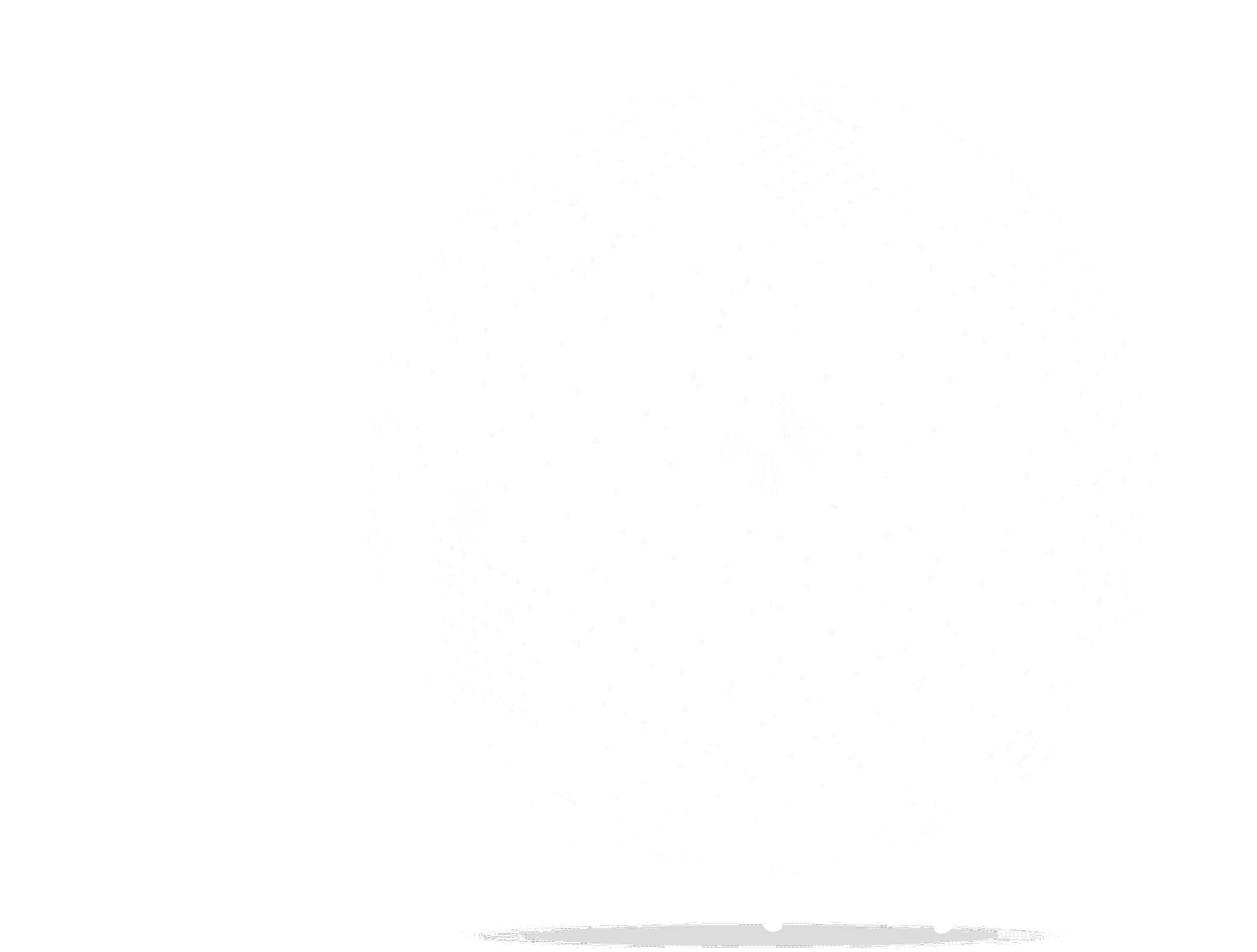
Open and receptive – the BestPractice Partner Network of Staufen AG
The BestPractice Partner Network of Staufen AG represents companies that have created beacons and BestPractice solutions in their organization and processes. They are market leaders, technology leaders or hidden champions who open their work gates to other companies to report on the challenges and results of their transformation.
The BestPractice visits serve participants to exchange in detail and constructively with the managers of BestPractice companies and to benefit from their experiences, successes and failures.
Staufen AG offers BestPractice visits in different formats and on different key topics and, on request, also adapted to the individual needs of interested customers. What would you like to see? Which example would inspire you in your current situation or help you to gain even more confidence in your transformation process?
Magazine Article about Virtual BestPractice Tour
“Lean Expedition” in China, Europe and Brazil
You might also be interested in

Endress+Hauser
Endress+Hauser is a global leader in measurement instrumentation, services and solutions for industrial process engineering, optimizing processes in terms of economic efficiency, safety and environmental impact.
Read more
Leadership Excellence: Around the world in 480 minutes
Transformation of the economy and society is gaining more and more momentum. The dynamics of change require “effective leadership” from a company’s management – especially in times of rapidly changing conditions. All levels of a company are put to the test: What is being preserved and what needs to be changed to ensure the success of the organization? How can employees get involved in achieving the company’s goals in a climate of cooperation and trust?
Read more
Best Practice Live
Exclusively for you, we are opening the gates to excellent businesses – our BestPractice partners. Benefit from case studies of successful businesses.
Read more