
The family-owned company Hargassner has been on the market for more than 38 years. With over 140,000 satisfied customers around the world, it has made a name for itself as a pioneer in environmentally friendly heating with renewable energy. This biomass heating technology specialist employs more than 700 qualified workers and has a production capacity of over 25,000 boilers per year. Its intelligent wood chip, pellet & firewood heating systems are exported to 36 countries.
The company’s successful history began with a promise that Anton Hargassner made to his wife. “I’ll build you a heating system that you never need to stoke!” For all the heating technology options at the time were completely unsatisfactory in the mind of this tinkerer and entrepreneur. A lot has happened since then. Four decades later, the Hargassner brand stands for innovative heating systems with the lowest emission values and the greatest efficiency.
Meanwhile, Markus and Anton Junior have followed in the footsteps of their father, Anton, who was always on the go. Carrying on his pioneering spirit, they constantly examine proven ideas and seek better solutions in order to keep advancing biological heating.
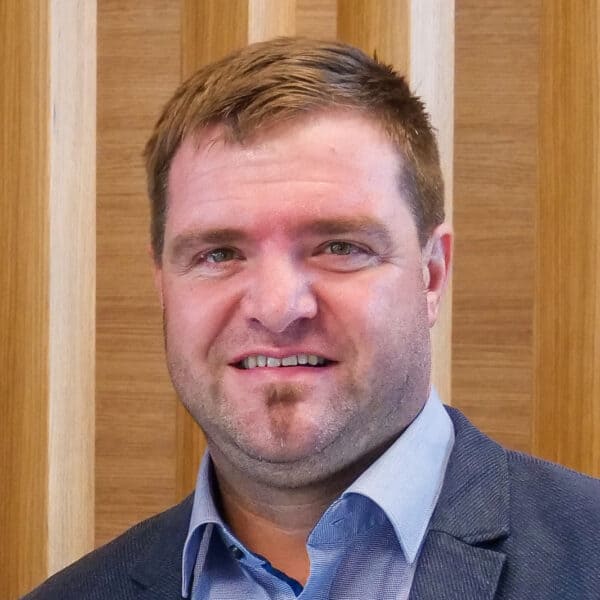
Markus Hargassner
Managing Director
HARGASSNER Ges mbH
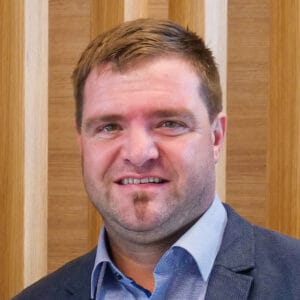
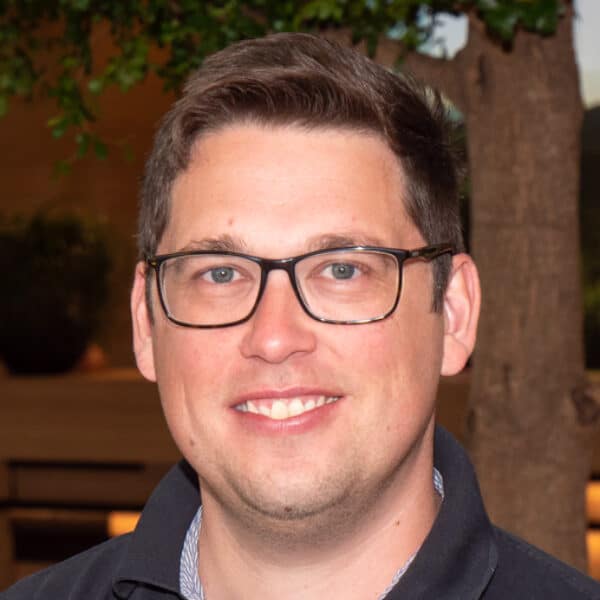
Mathias Hasibeder
Assembly Manager
HARGASSNER Ges mbH
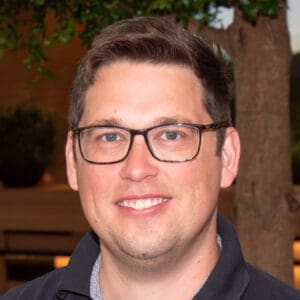
Experience biomass live
“Sustainability,” says Markus Hargassner, “is part of our DNA and visible everywhere. For example, we do our own forest management. Every heating system that leaves our factory is based on timber from our forest.” In 2016, Hargassner created a 25,000 sq m energy park with poplars, meadows, elephant and sida grass in order to conduct experiments with new kinds of fuel, always on the hunt for new heating materials for the future.
In 2019, the company was expanded to include the 6000 sq m Energy World. A new training center was built, a customer center with an impressive biomass world and state-of-the-art office facilities. Right in the middle: the “village square,” which employees use for little breaks and a lot of communicative exchange.
Markus Hargassner is proud of the building expansion. “We asked ourselves if we should go to our customers – or if our customers should come to us in order to experience how we exemplify sustainability. We value the proximity to our customers; we listen to them in order to learn what motivates them and what they want. Ideas for further innovations and improvements come from these conversations.”
Furthermore, Energy World is a commitment to the region and to the employees. As a family entrepreneur, Markus Hargassner regards this as his duty. “Here in the region, we are a preferred employer, probably also because we make sure that the working conditions are good; we’re almost a family.”
I was already familiar with Lean Management methods, nevertheless I was surprised by how we, with the help of Staufen, were able to achieve a significant improvement in balancing and lead times.
MATHIAS HASIBEDER
Assembly Manager at HARGASSNER Ges mbH
Planning of a new assembly hall
The company believes it is on the right path, but the tempo of development keeps reminding people to pause in order to consider new, still better solutions. When it was time to plan a new assembly hall, the heating system manufacturer regarded this as an opportunity to take another careful look at its assembly line. With Werner Laub and Staufen AG, it didn’t take long to find a partner who understood the company’s philosophy and could support it expertly and as a partner during further development.
The planning of the new assembly hall offered the opportunity to examine the existing production system once again and to re-establish it according to lean principles. After extensive analyses of existing production and logistics processes, an optimal rough concept for the new assembly hall was developed, one that implements a sensible chaining of assembly and both upstream and downstream processes.
With the setup of a lighthouse area for the assembly of the 20 – 32 kW Nano-Pellet boiler according to lean principles, it was possible to sketch out significantly higher area productivity. The insights gained were used to design the fine planning of the work systems and implement logistics processes in the new hall.
Assembly Manager Mathias Hasibeder expresses his satisfaction about the course of the project: “I was already familiar with Lean Management methods, but I was surprised how, with the help of Staufen, we were able to achieve another significant improvement in balancing and lead times.”
Striving for perfection
While the planning and implementation of the new assembly line were in the works, employees were trained as lean experts and Shop Floor Management was introduced for continuous process improvement purposes in order to anchor the changes in the process for the long term.
In the future, these good experiences from assembly should also be transferred to other areas. The Hargassner brothers are convinced that the Lean Management methods are the right solution and they are motivated to establish a comprehensive improvement culture at the company. Markus Hargassner grins: “My brother and I are passionate technicians. It’s hard for us to accept solutions that aren’t perfect.”
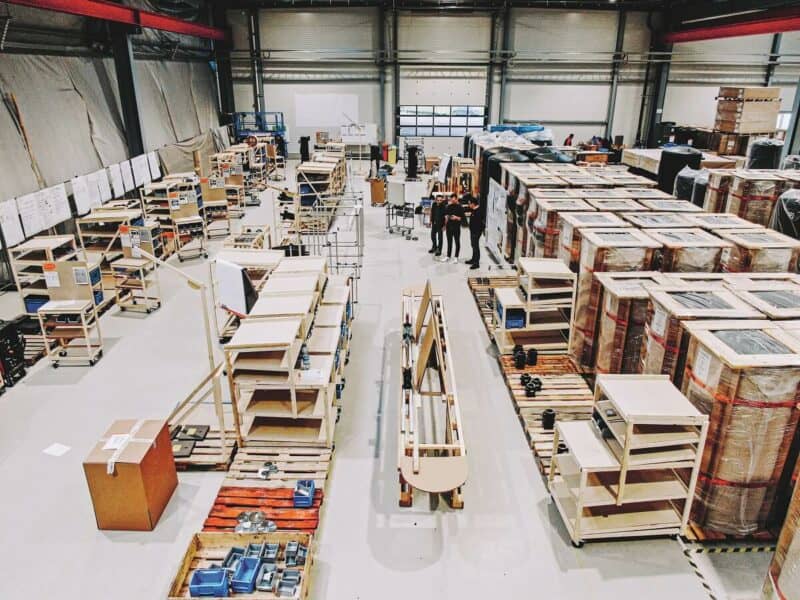
of the assembly concepts
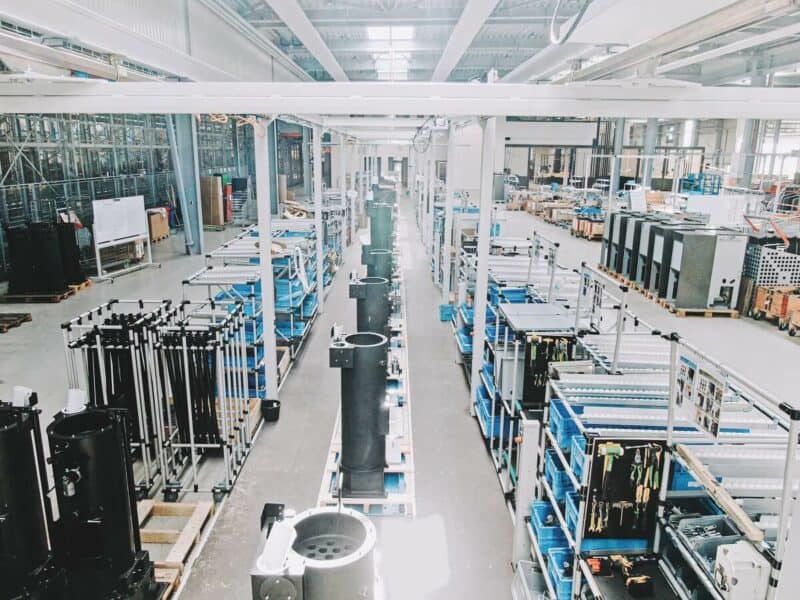
The company
The family-owned company Hargassner has been on the market for more than 38 years. It has made a name for itself as a pioneer in environmentally friendly heating with renewable energy.
> 700
EMPLOYEES
36
exported Countries
25,000
boilers per year
Magazine Article about Hargassner
How to fuel growth with sustainability
You might also be interested in
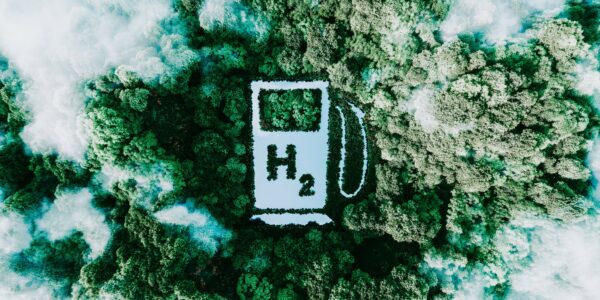
“The energy-political revolution will not be able to escape hydrogen”
The Solidpower Group is one of the world’s leading companies in the high-temperature fuel cell technology (SOFC, Solid Oxide Fuel Cells). At locations in Italy, Germany, Switzerland, and Australia, the group manufactures and sells fuel cell systems for power and heat generation in residential and commercial buildings.
Read more
“Our goal is not to spend a cent more on electricity in the future.”
As a supplier of die casting technologies, Oskar Frech GmbH + Co. KG operates in an energy-intensive environment. Thanks to efficiency improvements and sustainable planning, the hidden champion was able to drastically reduce its energy consumption. Managing Director Dr. Tim Nikolaou explains in an interview how the transformation succeeded and what role lean management plays in the green transformation.
Read more