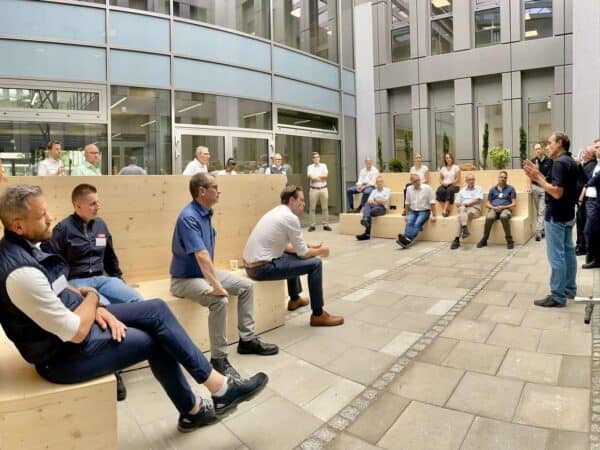
Experiences, stumbling Blocks and proven Solutions
When the BestPractice Partner Circle comes together, this is where market leaders, technology leaders and hidden champions meet.
The exclusive BestPractice Partner Circle hosted by Staufen AG and made up of around 40 companies in the German-speaking region, was finally able to convene in person at the invitation by BMW AG located in Landshut, Germany, also a member of the partner circle. The attendees were given the opportunity to reflect on common best cases, learn from each other and openly exchange ideas.
Core topic: The value-added production system
The value-added production system creates the foundation for successful business transformation by integrating lean and digital approaches. Executives and lean leaders from BMW AG spoke about experiences, stumbling blocks and proven solutions on their lean journey before inviting attendees on a plant tour.
The value-added production system is the heart of the production system at the BMW Group
The underlying idea behind the value-added production systemis to prevent waste, work efficiently and design workplaces ergonomically. The WPS Center of the BMW Group includes a learning workshop covering a space of 1,500 m².
Key factors in the changes have been the successful application of lean methods such as linking assembly processes in a one-piece flow, establishing Kanban control loops for material supply and supplying products by means of tugger trains.
Besides the physical lean transformation, BMW in Landshut is also actively implementing a cultural change among employees and executives – by introducing a new work organization with foremen (Japanese “hanchos”) as CIP implementers and problem solvers.
Attendees experience a lean journey
During the introductory talk, the implementation of the value-added production system (WPS) and the corresponding implementation of the new work organization at the Landshut site was presented. The tour of the process boards, control boards, and logistics processes provided practical proof of successful production in one-piece flow based on customer demand.
With increasing complexities that a traditional, analog approach of value stream mapping and our brains can no longer grasp, process mining is the solution. This was the consensus of the second agenda item, the topic “Outlook and further development of WPS”.
In the subsequent live presentation, the participating company managers were given a comprehensive insight into the system worlds. Benefits and lessons learned so far in the Smart Maintenance App development were revealed.
The final discussion emphasized that employees, as experts in their field, should be given responsibility on the shop floor. They become a key element in the continuous improvement process (CIP) by being invited to optimize, create and innovate.
You might also be interested in

Best Practice Live
Exclusively for you, we are opening the gates to excellent businesses – our BestPractice partners. Benefit from case studies of successful businesses.
Read more